【汽车产经网】2016年1月21日,位于浦东金桥的上汽通用凯迪拉克工厂正式竣工投产,同时,凯迪拉克旗舰轿车CT6也正式下线。9个月前的2015年4月19日,上汽通用的“创领2020-上汽通用汽车之夜”正是在这座工厂里举行。当天,上汽通用公布了其面向未来5年的战略规划。规划指出,2020年,凯迪拉克要在豪华车市场实现10%的市场占有率。如今凯迪拉克工厂投产、CT6即将上市,上汽通用凯迪拉克品牌似乎已经蓄势待发。
投资80亿 “最贵工厂”年产能16万台
据了解,凯迪拉克工厂是上汽通用在上海几个工厂中的最为先进的工厂,包含车身车间、涂装车间、总装车间、高速试车道、联合站房等一系列配套设施。一期总投资80亿元人民币,规划年产能16万台,每万台产能投资高达5亿元,这一数字远高于北京奔驰的NGCC工厂和华晨宝马铁西工厂。
2015年4月,北京奔驰NGCC工厂投产,总投资额为7.2亿欧元(约51亿人民币),整车产能将达到25万辆,平均每万台产能投资额为2亿元;2012年5月,华晨宝马铁西工厂正式开业,总投资15亿欧元(约107亿人民币),产能最高达40万辆,平均每万台产能投资2.7亿元。而凯迪拉克工厂每万台产能投资高达5亿元,它也因此成为“最贵豪华车工厂”。
最贵工厂贵在自动化水平高
一位车企内部研发人员对此评价说,“这样的投入在业内确实是比较高的。现在汽车企业新建工厂时,都越来越看重自动化水平的提升。自动化水平的提升是比较烧钱的,但能给企业带来不菲的收益,一方面可以节约人力成本,另一方面能提升良品率,减少次品和浪费。”
正如这位研发人员所说,“最贵工厂”最大的“过人之处”便是其自动化水平。据了解,凯迪拉克工厂有着国内首个具备全铝车身制造能力的车身车间,车间内有钢、铝两条全自动化生产线,有机器人386台,可实现车身连接技术100%的自动化。这一数据远高于奇瑞捷豹路虎常熟工厂307台机器人和85%的自动化率。
此外,在焊装车间,凯迪拉克工厂还在国内首次引进了铝激光钎焊技术,同时还大规模应用了自攻螺接、自冲铆接等业内领先的车身冷连接工艺。
涂装车间是凯迪拉克工厂最引以为傲的车间,整个涂装车间没有一座混凝土高烟囱,这在国内尚属首家。据了解,这里喷漆、涂胶100%由机器人完成,同时,该工厂还采用了薄膜前处理、高泳透力电泳、二道色漆、有色清漆、液态可喷涂隔音垫等一系列全球领先的涂装工艺。
凯迪拉克的总装车间更是充分体现了现代化汽车工厂集柔性与智能于一体的先进性。这里不仅能够支持7款车型柔性拼装,而且通过智能物联网系统,可以追溯每一个关键紧固点的扭矩信息,构建起世界级数字化装配体系。
国产CT6即将上市 迎战宝马新7系
作为“最贵工厂”下线的首款产品,凯迪拉克CT6是目前上汽通用国产车中级别最高的豪华轿车。
据了解,凯迪拉克CT6采用了业界领先的高强度、轻量化车身设计:车身材料融合了11种不同的轻量化材质,其中铝材占比超过57%;借助多项宇航级车身工艺,全面提升了车身的强度、性能及效能,保证车体坚固的同时自重却大幅降低;此外,凯迪拉克工厂还在国内首次应用二道色漆和有色清漆两项全球领先的涂装工艺。
2015年4月19日,上汽通用公布了其面向未来的5年的战略规划。根据规划,到2020年凯迪拉克要在豪华车市场实现10%的市场占有率,成为豪华车市场主流品牌,这意味凯迪拉克2020年的销量将达到20万辆以上。即将上市的凯迪拉克CT6,预计将成为上汽通用实现这一目标的重要“武器”。
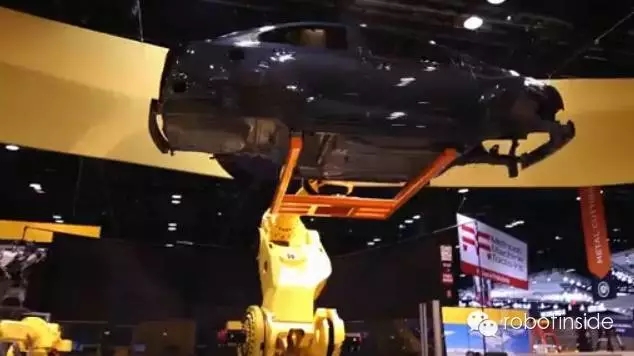
延伸阅读:发那科与思科欲打造“不停工工厂”,以工业机器人零停机为终极目标
发那科和思科系统日本2016年1月21日宣布,将在旨在提高工业机器人开工率的解决方案方面展开合作。发那科将使用思科系统日本的网络设备及系统,向使用发那科机器人的用户提供解决方案。将力争于2016年夏季到秋季期间开始提供解决方案。该解决方案可在工场中运转的机器人发生故障之前,根据运转数据的分析结果来预测故障的种类及发生时间。这样便可事先采取更换部件等适当应对措施,从而减少停机时间并降低成本。据某汽车厂商推算,在意外停机时间内,每分钟会平均产生200万日元的损失。
据发那科专务董事、机器人事业本部长稻叶清典介绍,以往大多在发生故障后调查原因,这种方法在减少停机时间上存在极限。而发那科的目标是通过事先预测,最终“使停机时间减少为零”(稻叶清典)。因此,发那科将该解决方案称为“零停机时间(ZDT)解决方案”。即便是发生了故障,该解决方案也可通过分析运转数据来迅速查明故障原因,可将停机时间减少至最小限度。
在汽车大厂商的工厂成功实施验证
在此次发布合作消息之前,发那科和思科系统日本两公司利用12个月的时间,在汽车大厂商位于北美的工厂实施了ZDT解决方案的中试项目。在这一期间,成功将机器或生产设备的停机时间减少为零,提高了综合设备效率(OEE:Overall Equipment Efficiency)。
ZDT解决方案将机器人配备的电机及传感器等的数据收集至设置在工厂中的服务器(ZDT服务器),利用ZDT服务器来分析数据。当捕捉到故障预兆时,就会发出警报。并且还可将数据发送至发那科的数据中心,实施更深度的分析。该解决方案将作为选配服务,向使用发那科机器人的用户提供。价格尚未公布。目前该解决方案还不能运用发那科一直在致力开发的人工智能技术(AI),但今后“将使人工判断操作能够由AI来替代”(稻叶清典)。
思科系统日本为实现分散处理大量数据的“边缘计算”提供相关网络设备及服务器。发那科的数据中心也是作为私有云在思科系统日本的服务器上构筑的。